Éviter les pannes et les défaillances est essentiel pour assurer le bon fonctionnement des systèmes, qu’ils soient industriels, informatiques ou même liés à la vie quotidienne. La prévention est la clé pour anticiper les dysfonctionnements, permettant ainsi de maintenir un niveau de performance optimal. Dans cet article, des stratégies, des conseils et des outils seront présentés afin de minimiser les risques de défaillances.
Comprendre les dysfonctionnements
La première étape pour prévenir les dysfonctionnements est de comprendre les types et origines des pannes qui peuvent survenir. Les dysfonctionnements peuvent être causés par divers facteurs, allant de l’usure matérielle aux erreurs humaines. Identifier ces causes peut aider à anticiper et à mettre en place des mesures préventives.
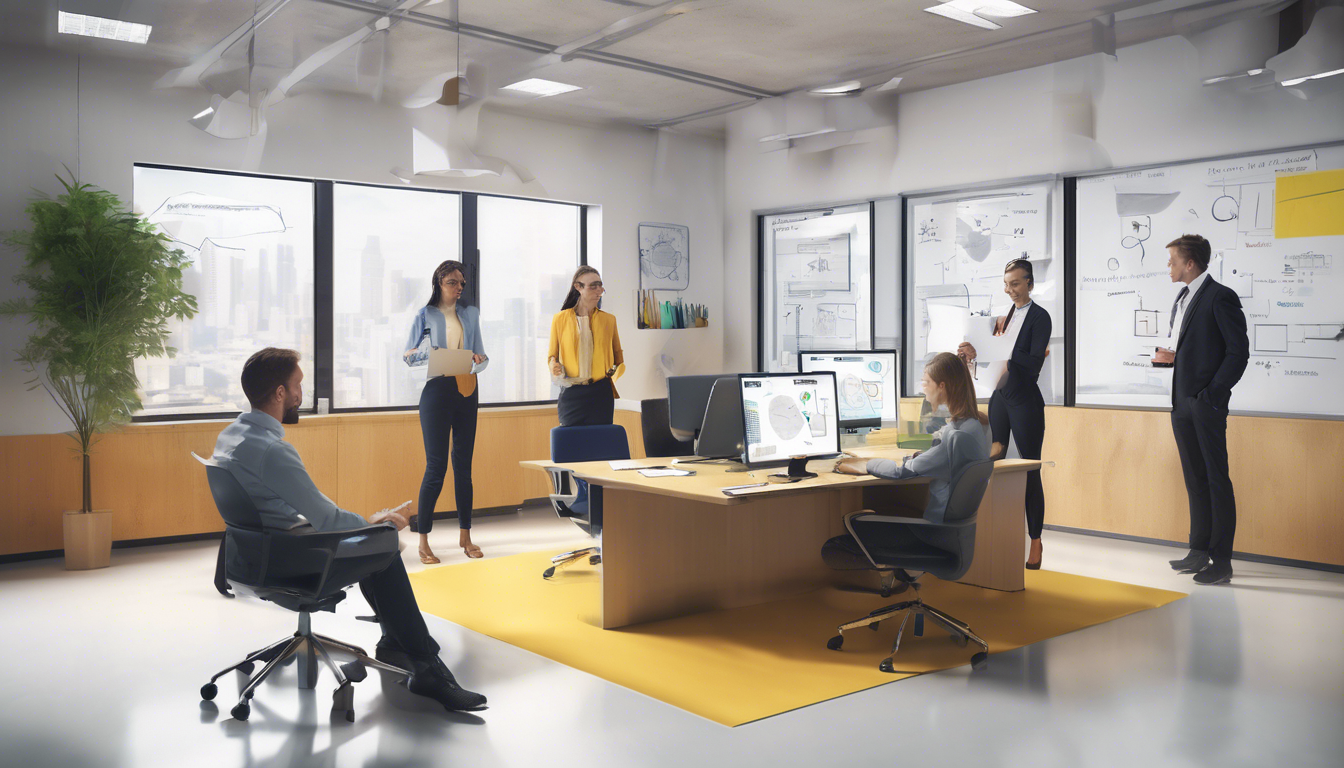
Types de dysfonctionnements matériels
Les dysfonctionnements matériels peuvent être classifiés en plusieurs catégories :
- Dysfonctionnements mécaniques : souvent causés par l’usure des pièces ou par des dommages physiques.
- Dysfonctionnements électroniques : peuvent survenir à cause de surcoupures de courant ou de courts-circuits.
- Erreurs logicielles : qui peuvent être dues à des mises à jour inappropriées ou à des conflits de logiciels.
- Facteurs environnementaux : tels que la température excessive ou l’humidité qui peuvent altérer le fonctionnement des appareils.
Effectuer une maintenance régulière
Un entretien régulier est indispensable pour assurer la longévité de tout équipement. Cela inclut des vérifications visuelles fréquentes et l’application des recommandations du fabricant concernant la maintenance préventive.
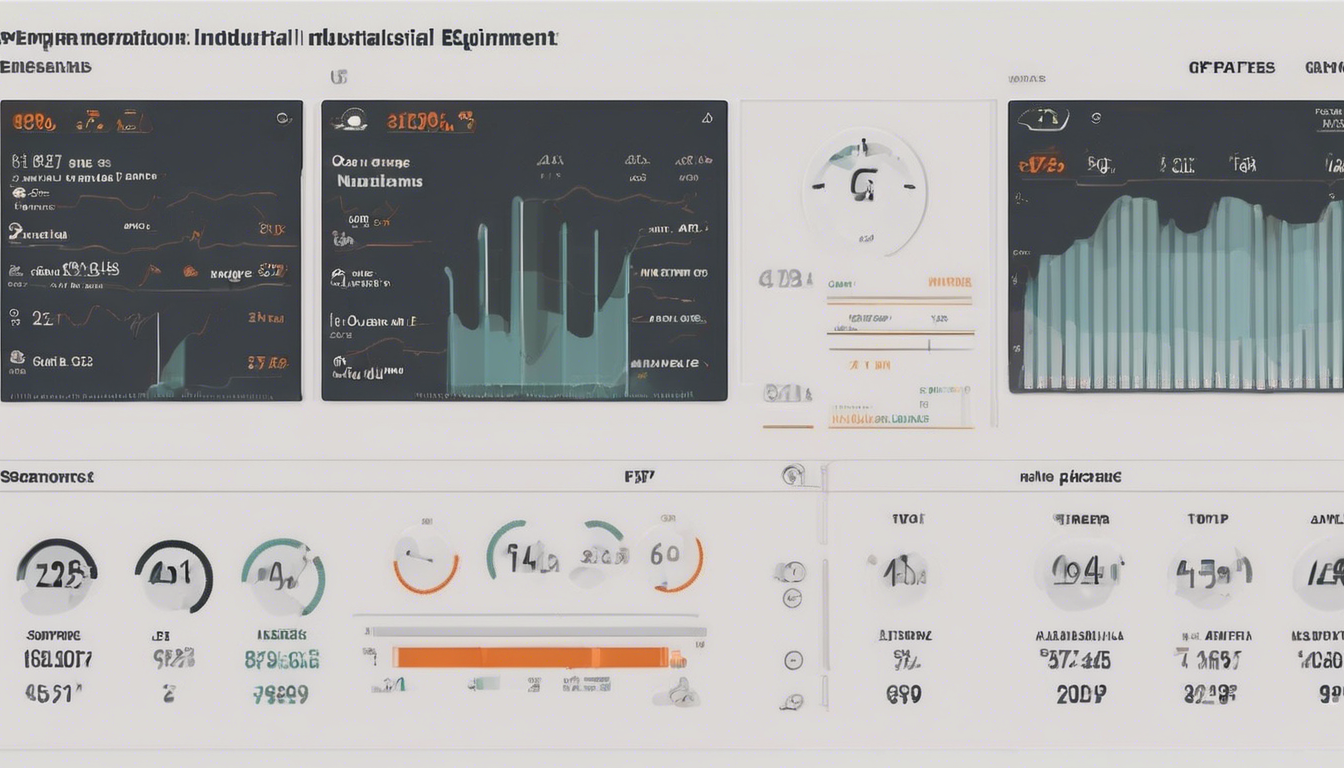
Les étapes de la maintenance préventive
Pour éviter les pannes, il est crucial de suivre un programme de maintenance préventive. Voici quelques étapes clés :
- Inspection régulière : vérifier l’état des équipements pour détecter d’éventuels problèmes avant qu’ils ne s’aggravent.
- Remplacement des pièces usées : anticiper les réparations en remplaçant les composants avant leur défaillance.
- Formation des utilisateurs : s’assurer que tous les opérateurs sont bien formés à l’utilisation correcte des équipements.
Surveillance des indicateurs de performance
Une surveillance proactive des indicateurs de performance permet de détecter rapidement les anomalies et d’agir avant qu’elles ne causent des dysfonctionnements majeurs. Cela implique le suivi des paramètres opérationnels tels que la consommation énergétique, le temps de fonctionnement et le degré d’usure des composants.
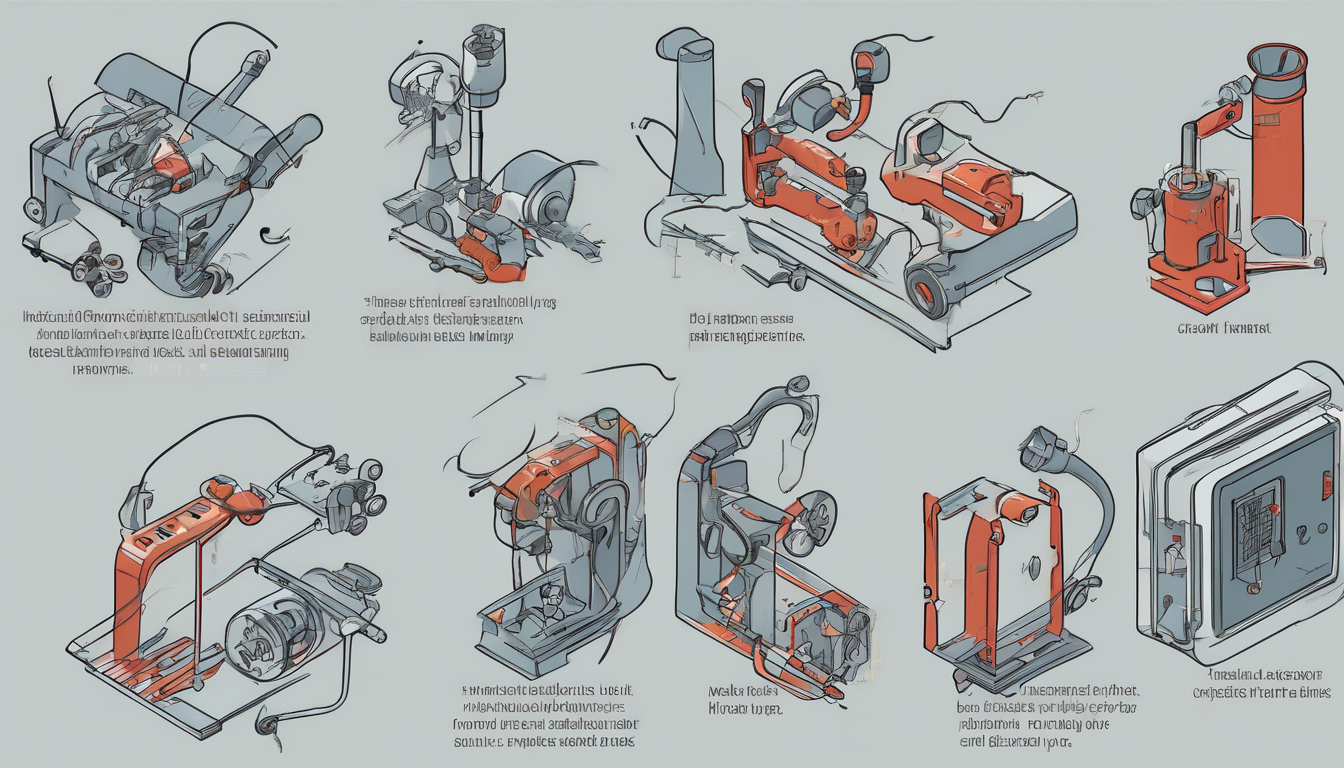
Les indicateurs clés à surveiller
Voici quelques indicateurs essentiels à surveiller :
- Temps moyen entre les pannes (MTBF) : un indicateur crucial pour évaluer la fiabilité d’un système.
- Consommation énergétique : une augmentation soudaine peut indiquer un problème sous-jacent.
- État des pièces : surveiller l’usure des pièces sensibles peut prévenir les pannes soudaines.
Former les opérateurs et techniciens
La formation continue des employés est essentielle pour minimiser les risques de défaillance. Un personnel bien formé est en mesure de reconnaître les problèmes avant qu’ils ne se transforment en pannes graves.
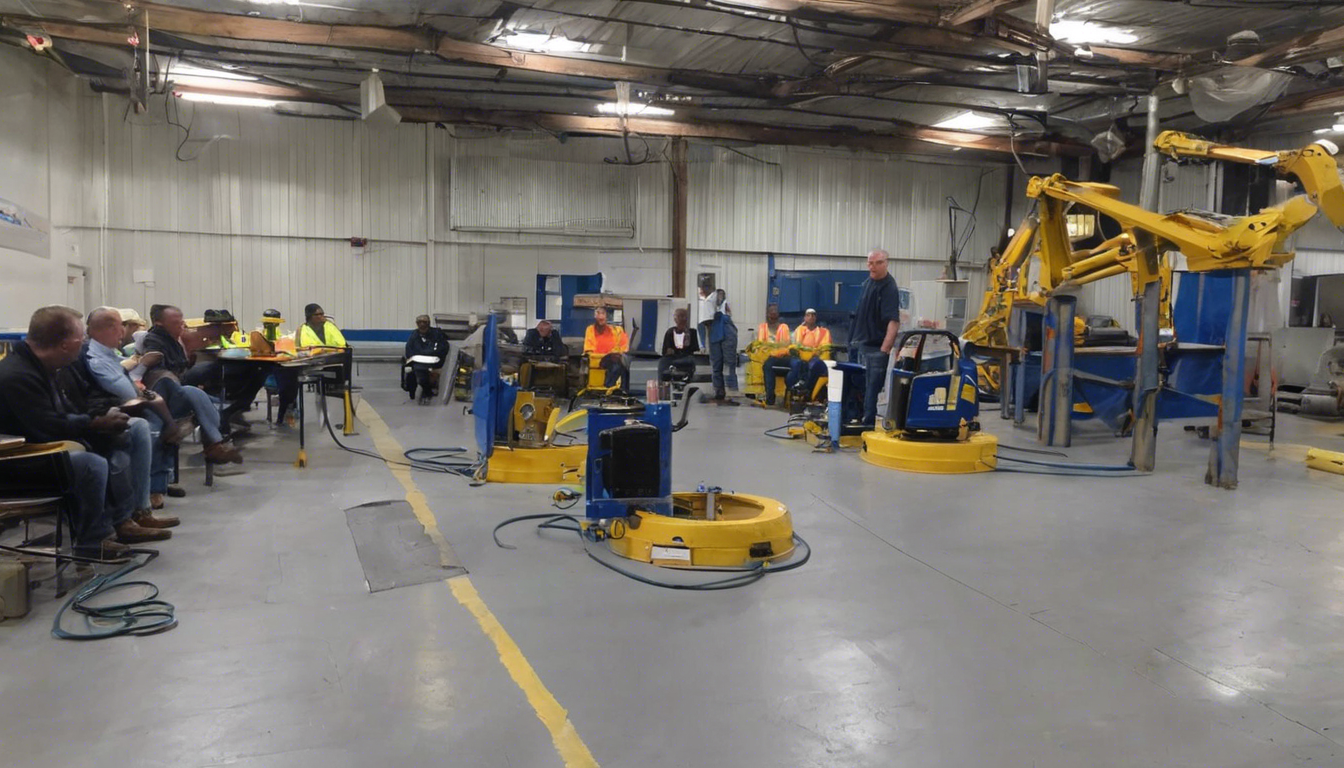
Programmes de formation efficaces
Pour maximiser l’efficacité de la formation, il est recommandé de :
- Mettre en place des sessions régulières : s’assurer que le personnel est au courant des dernières procédures et des risques.
- Utiliser des outils pédagogiques variés : manuels, vidéos et simulations peuvent aider à améliorer l’apprentissage.
- Encourager la communication : un climat où les techniciens se sentent à l’aise pour signaler des erreurs peut améliorer l’ensemble du système.
Mettre en place un système de suivi des défaillances
Avoir un système efficace pour suivre les défaillances et analyser les données provenant des équipements permet de répondre rapidement aux problèmes et d’améliorer continuellement les processus.
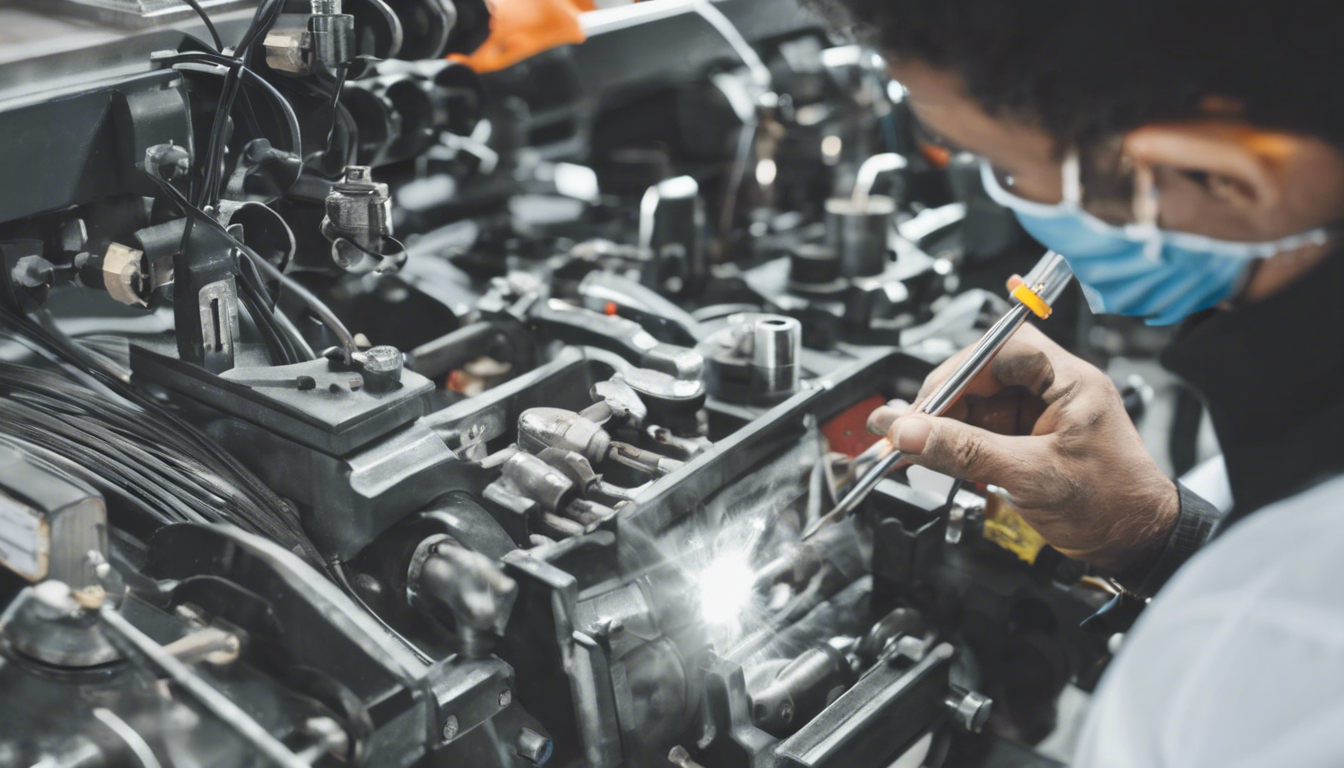
Les éléments d’un bon système de suivi
Pour assurer l’efficacité d’un système de suivi, il doit comporter :
- Des indicateurs clairs : permettre aux équipes de comprendre rapidement l’état des équipements.
- Une bonne communication : assurer une remontée d’informations rapide vers les techniciens.
- Des analyses régulières : effectuer des analyses des données pour identifier les tendances et les points à améliorer.
Conclusions sur la prévention des dysfonctionnements
La mise en œuvre de ces stratégies de prévention permet non seulement d’éviter les dysfonctionnements, mais contribue également à instaurer un environnement de travail plus sûr et plus efficace. En adoptant une approche proactive face aux pannes potentielles, il est possible de garantir la continuité des opérations et d’optimiser l’utilisation des équipements.